R1002B/R2002B
Rotary Evaporator
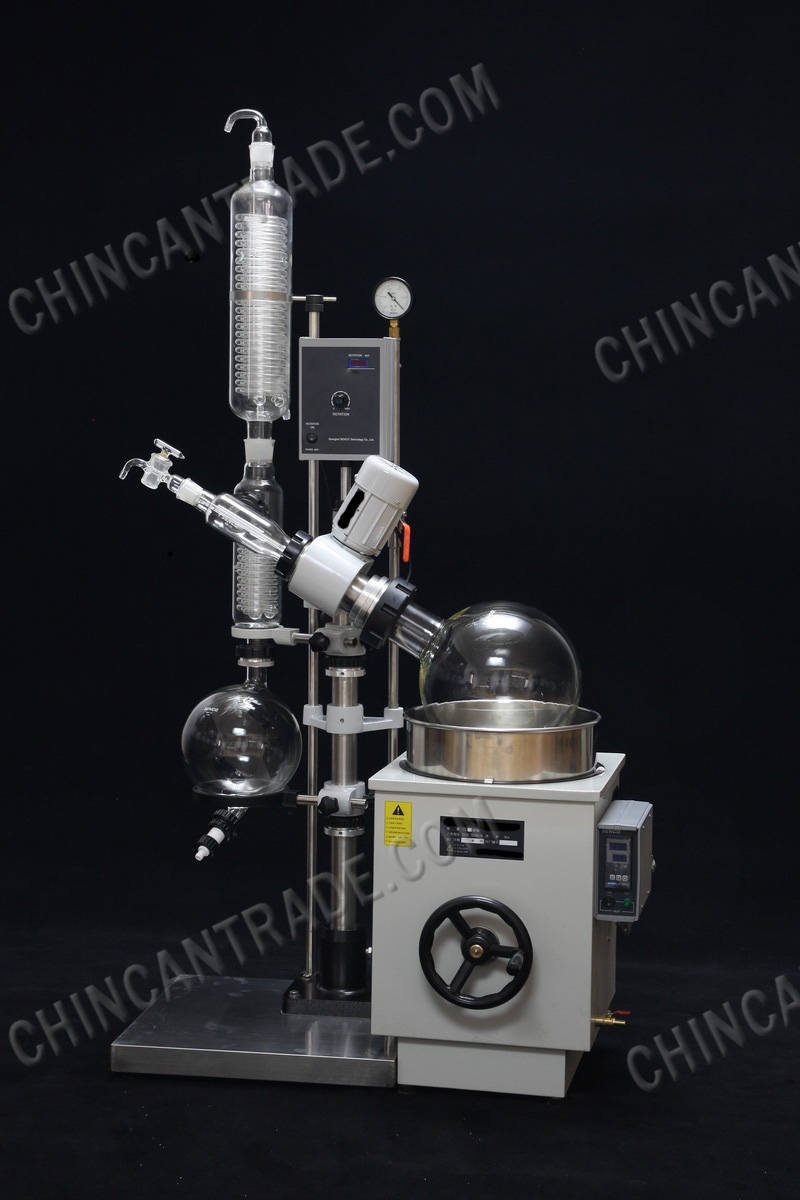
In Pilot Production Evaporating Field
With our unique tandem receiving technology, Solvent Discharge no longer need to stop evaporation
process, to release and repump system vacuum. The technology allows real continuous work without
vacuum wave, which obviously increases productivity, simplifies system receiving structure and
improves sealing performance. (for K series)
Features
1. PTFE Charging Valve
New structure and material applied, is able to offer purely clean charging process and durable use
experience.
2. Flange Quick Press Ring
One-piece quick clip design. Offer new experience on easy, reliable, and high sealing connection
for flanges (no tools required).
3. PTFE Cork (Patent No. 01253089.1)
Senco patent structure. Cork is anti-corrosion, no vacuum grease, no pollution to solvent received.
.jpg)
.jpg)
.jpg)
4. Anti-corrosion & Wearable Sealing System
Specially designed and precisely manufactured. Enable system ultimate vacuum rate reaching 133Pa.
90% users do not need to replace rotary seal in one year.
5. Ex-proof Modification (Optional)
Offer EX proof upgrade on Motor, Control Boxes of rotation and heating, Wiring, and Safety measures per
user needs. Ex level reaches ExdIIBT4.
6. Bumping Tube (Optional)
Preventing unexpected solution bumping into receiving flask.
7. Cold Trap Protection (Optional)
Trapping escaped corrosive/harmful vapor so to protect vacuum pump and people health. Avoid vacuum
pump liquid flow back to system.
8. Flask Unload Handler (Optional)
Specially designed for handling and unloading big capacity evaporating flask, is one useful and popular
optional tool.
.jpg)
.jpg)
.jpg)
.jpg)
Specifications
Standard Model | R1002B | R2002B | R2005KB | R5005B | R5005KB |
Relevant Model | R1002D/ | R2002D/ | R2005KD | R5005D/ | R5005KD |
R1002B(Ex) | R2002B(Ex) | R2005K2B | R5005B(Ex) | R5005K2B | |
R2002S | R2005KB(Ex) | R5005S | R5005KB(Ex) | ||
R2005KS | R5005KS | ||||
Evaporating Flask (L) | 10L/ F95 | 20L/ F95 | 20L/ F120 | 50L/ F120 | 50L/ F120 |
Receiving Flask (L) |
5L,Bottom Discharge | 10L, Bottom Discharge | 20L, Bottom Discharge | ||
Condensing Surface (m2) |
0.57 | 1 | 1 | 1.5 | 1.5 |
Rotation Speed (rpm) |
3-110 | ||||
Evaporating Speed (H2O) |
3L/h | 5L/h | 9L/h | ||
Reachable Vacuum Rate |
< 133Pa (1.33mbar, 1 Torr) | ||||
Bath Power (kW) | 3 / 2(Ex) | 5 / 3.6(Ex) | 9 / 6(Ex) | ||
Static Temp. Control Range & Wave (℃) |
0-99(180) ±0.2 | ||||
Bath Size (cm), | Ø35x25H, 22L, | Ø45x27H, 40L, | Ø45x27H, 40L, | Ø55x32H, 70L, | Ø55x32H, 70L, |
Capacity, Material | SUS304 | SUS304 | SUS304 | SUS304 | SUS304 |
Power | 220V, 50/60Hz | 380V, 3-p, 50/60Hz | |||
Dimensions (cm) | 95x50x180H | 110x60x210H | 110x65x190H | 130x80x185H | 130x80x200H |
**Max evaporating speed is affected by operation settings and the performances and matching levels
of supporting equipment.
Functional Configurations
Model | R1002B | R2002B | R2005KB | R5005B | R5005KB |
Charge Valve | Glass | PTFE | |||
PTFE Discharge Valve | PTFE | ||||
PTFE Rotary Seal Assembly | YES | ||||
Overall Flange Joints | NO | NO | YES | YES | YES |
Taper Joint PTFE Sleeve | YES | YES | NO NEED | ||
Frequency Conversion | YES | ||||
Speed Control | YES | ||||
Vacuum Meter | YES | ||||
Throttle Valve for Vacuum | YES | ||||
Cooling Circulation Nozzle Thread Adaptor | NO | NO | YES | YES | YES |
Thermometer Neck for Vapor | NO | NO | YES | YES | YES |
Tandem Type Continuous Receiving | NO | NO | YES | NO | YES |
Digital Display | Bath Temp., Rotation Speed | ||||
Evaporating Flask Unload Handler | NO | OPTIONAL | |||
Ex-proof Motor | OPTIONAL | ||||
Steam Heating | NO | OPTIONAL | |||
Cold Trap Protection System | NO | NO | OPTIONAL | ||
Bumping System | NO | NO | OPTIONAL | NO | OPTIONAL |
Big Evaporation Neck upgrade | NO | NO | NO | OPTIONAL | OPTIONAL |
F145 | F145 | ||||
Optional Evaporating Flask | 5L | 5L 10L | 10L 20L |
Safety Features
Model | R1002B | R2002B | R2005KB | R5005B | R5005KB |
Over-current Protection | YES | ||||
No-spark Electronic Control | YES | ||||
Ex-proof Upgrade* | Ex-proof Modification on Motor, Rotation & Heating Control; Lower heating | ||||
power density; Equip Dry Heat and Overheat Cut-off Protector |
Note: Some specifications of relevant models may have differences from that of standard model.
Details available at request.